BODY : Formula One racing cars are exceptionally fast, offering not only supreme acceleration and speed but also outstanding traction.
They combine leading edge engineering know-how with the latest structural materials technology.
No other material has been found superior to carbon fiber and carbon fiber composites for this purpose. It was first used in F1 car manufacture in 1981 and engineers have been using it ever since, for the past 40 years.
1981 was when the McLaren team introduced a carbon fiber monocoque chassis in their new MP4/1 car. In fact, this marked a major turning point in F1 for many reasons, including driver safety and racing car performance.
Why did no other material replace carbon fiber in F1 for the past 40 years?
Read on to discover some answers to this question.
Safety of F1 and carbon fiber composites
Contents [show]
Most people think that carbon fiber is used in F1 racing cars mainly because of its unmatched weight to stiffness ratio. However, safety and energy management are two other very important benefits of carbon fiber.
Many fatal accidents led designers to seek low weight materials that offered high absorption of impact energy.
The carbon fiber monocoque cockpit is the crucial element that contributes to safety. Monocoque design is used to construct the jointless chassis with the integral driver seat. Monocoque consists of a monolith, or structural single skin, similar to nature’s design of an egg.
Carbon Fiber Parts Manufacturing
In F1 monocoque design and manufacture with carbon fiber molding, the molds themselves are frequently made from carbon fiber. Prepreg technology is used to make many structural carbon fiber parts, which involves carbon fabrics impregnated with resin, called prepreg composites. The cockpit is built with several, or even several dozen, layers of carbon fiber prepregs and lightweight aluminum honeycomb core.
The whole then undergoes hardening in an autoclave under high pressure (116 psi or 8 bar) to eliminate any air and to compress the layers of composite materials. Eventually this process produces autoclave composites of carbon fiber that offer optimal strength for use in carbon fiber fabrication
Monocoque design provides superior impact related energy absorption. Monocoque structures that are now made from carbon fiber composites and aluminum honeycomb cores were originally made from steel and later from aluminum. However these metal structures have been replaced with carbon fiber since 1982 right up to the present day. A carbon fiber monocoque made using autoclave technology offers energy absorption far better than metal structures.
Energy absorption is categorized by Specific Energy Absorption (SEA) and is defined as the energy absorbed per unit mass of material.
Steel offers impact related energy absorption SEA of 12kJ/kg and aluminum about 20kJ/kg, whereas carbon fiber composite offers better SEA that can be as high as 40kJ/kg to 70kJ/kg.
Considering that the combination of monocoque cockpit and chassis weighs as little as 35 kg, we can easily see the answer to why carbon fiber composites are used widely for manufacturing F1 racing cars.
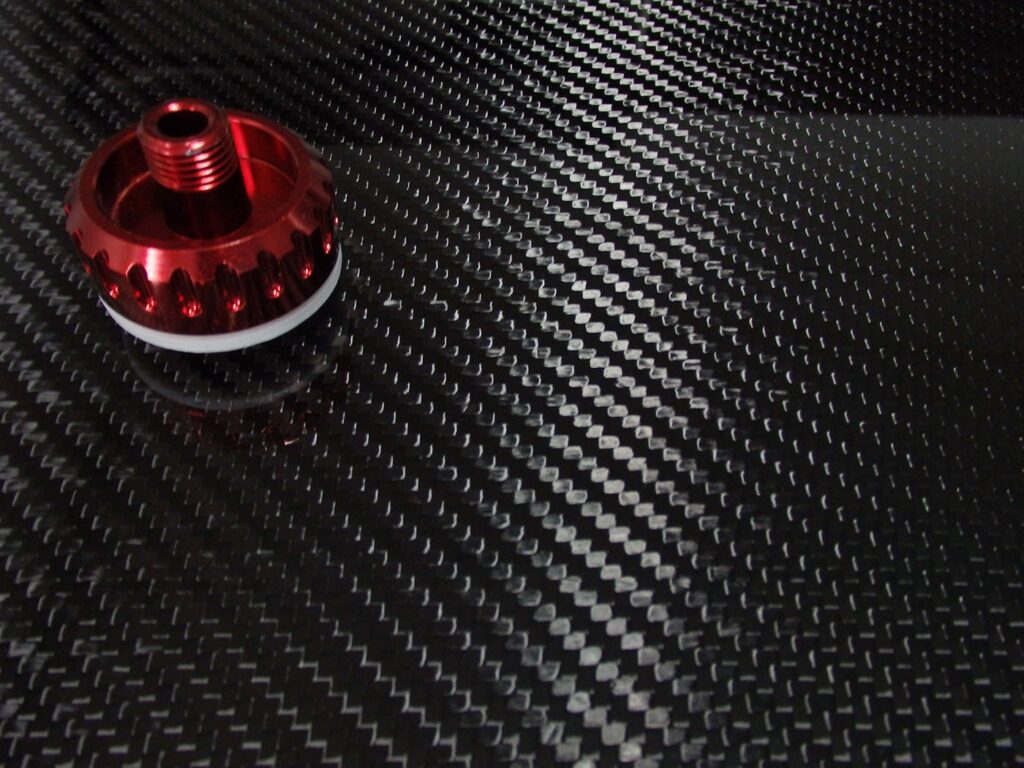
Statistics show dramatically improved safety
Monocoque design offers a crumple zone provided by the carbon fiber structure including an aluminum honeycomb core. During impact, it undergoes crushing and disintegrates into small parts that absorb the impact related energy and ensure driver safety.
The reality is that for over 25 years there has been no fatal accident in F1 racing. The last fatal accident was the sad death of Ayrton Senna in 1994. He suffered head serious injuries resulting from crashing into a wall at over 150 mph (240 km/h). The angle at which he hit the wall caused the right-front wheel to tear off upon impact, enter the cockpit and hit Senna on the front part of his helmet, causing fatal head injuries.
Carbon fiber’s low weight and high stiffness
In addition to the advantages of carbon fiber composites that are crucial for safety, it is the low weight and stiffness/rigidity ratio that play the crucial role. Carbon fiber offers the optimal weight and stiffness ratio of all materials available today – both metals and composites. As carbon fiber is 5 times lighter than steel, the weight of F1 racing cars was significantly reduced when this material was used.
Low weight provides better traction, performance, acceleration and shorter braking distance. That makes the car more agile in terms of handling.
Carbon fiber structural parts are the optimal solution for making racing cars. With this material, teams can build the fastest, agile, low weight cars possible.
Summary
To sum up, carbon fiber has played a crucial role since it was introduced to F1 racing. Use of this material improved driver safety and comfort, as well as performance. Until some other lighter and stronger composite is invented, it is carbon fiber composite that will be the leading material used in motorsport.
Seeing as for over 40 years it was impossible to replace carbon fiber with another better-performing material, does it mean that we have reached the limit in state-of-the-art technology?
Actually there is no simple answer to that question and only time will tell. It’s worth noting that carbon fiber used by McLaren back in the 1980s offered stiffness that was 3 times lower than what is currently available from today’s carbon fiber.
Carbon fiber is improving all the time.
Carbon fiber for your personal needs
Carbon fiber sheets and carbon fiber slabs.
Nowadays, anybody can obtain carbon fiber components designed specifically for a whole range of purposes from car parts to devices.
Carbon fiber is used for structural components of drones and other remote control (RC) devices and vehicles . You can order high gloss business cards made from ultra-thin carbon fiber sheets that can then easily be overprinted for a very distinctive look. It is used to produce a whole range of products from computer casings to mug mats.
The very material used in the manufacture of Formula One racing cars is widely available today. It’s used for DIY work and any projects where components offering low weight and high stiffness bring additional benefits or may even be necessary.
Today carbon fiber is available to everyone.